Kibu
Proving circular products are possible with locally manufactured tech.
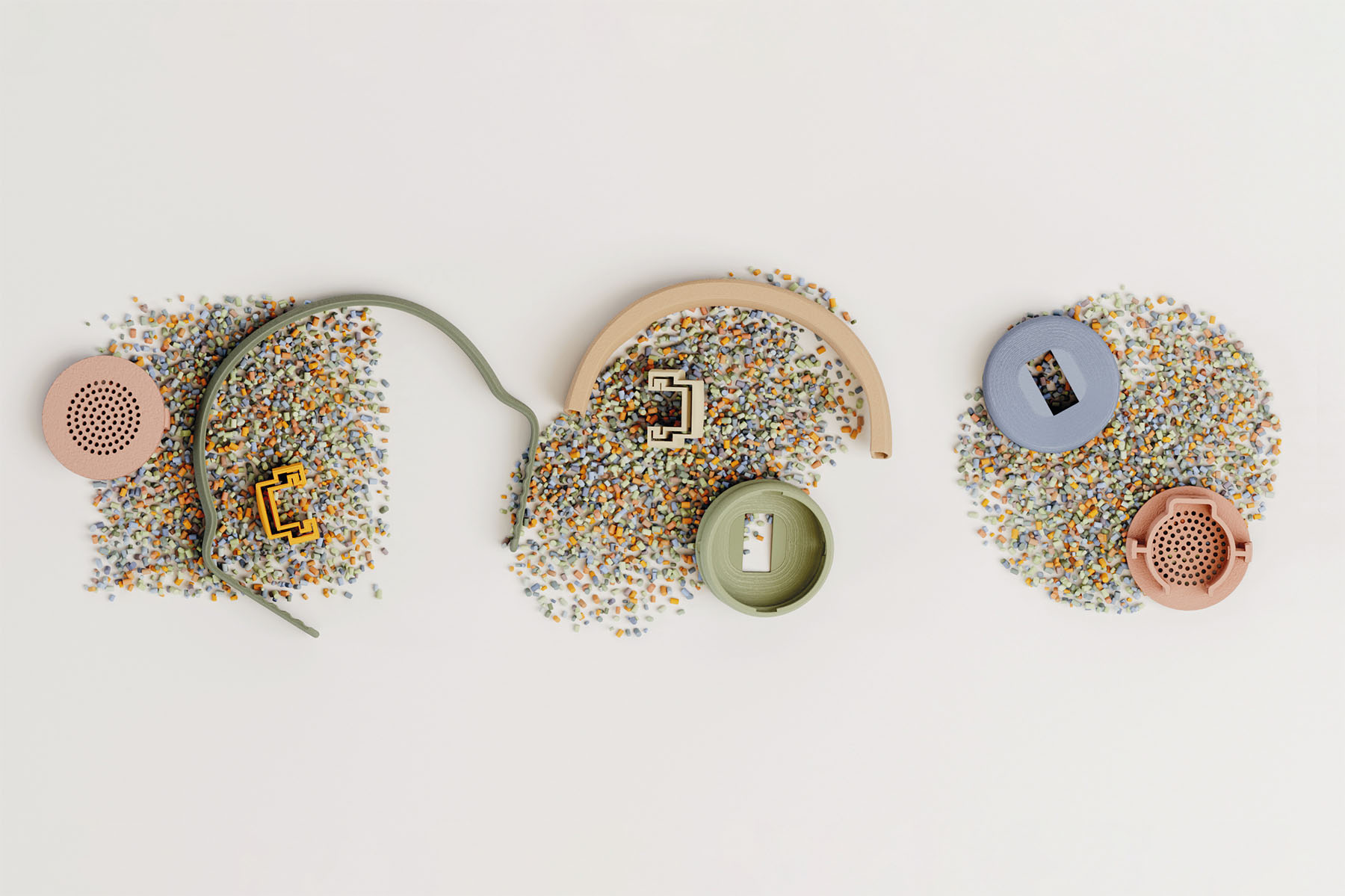
When a design studio and an additive manufacturing company became neighbours, it was obvious that they should collaborate. Morrama knows a lot about sustainable industrial design, and Batch. Works wants to improve manufacturing processes to make them more circular. This collaboration has provided an excellent chance to explore and innovate in the relatively new field of 3D print manufacturing.
“Children don't need noise cancellation, bluetooth or products that will last a lifetime, therefore designing simple solutions considered for end-of-life is key to tackling our e-waste problem. We see the ability to utilise circular materials that can be recycled and manufacturing closer to home as an obvious starting point.”
- Milo, Batch.Works
Engaging with the assembly of products provides children with a better understanding and appreciation of the objects they use and interact with. Through the playful construction experience of Kibu, children assemble their own headphones and build up the knowledge of how products is made, understanding the parts involved. Aimed at children 5-11 years old, the modular design and print-on-demand manufacture enables the headphones to colour customised, and adapted to changing head sizes.
With kids loving to pull, twist and take products apart, we’ve designed the Kibu headphones to embrace that. Children can pull the ear cups off, share with friends and slide them back on. If any aspect of the headphones are damaged or need to be sized up as the child grows – plastic parts can be sent back to Batch.Works, ground down, and made into new pairs of headphones.
Cleverly engineered, the headphones have a minimal number of parts, and have no need for screws, glue or any type of complex fixings. This means they can be assembled and disassembled little hands (and big ones too!).
The same minimalist approach has been taken to the electronics, using two modular PCB’s and two cables. The circuit boards are fabricated from Soluboard® , the worlds first recyclable PCB board, allowing electronic components to easily be recovered at the end of life.
From a manufacturing point of view, Kibu aims to demonstrate that local manufacture of technology products can be possible and transparent sustainability can be achieved without sacrificing beautiful design or user experience.
The challenge with 3D print manufacturing is speed. Whilst injection molded parts can be created in seconds, FDM parts are built layer-by-layer, taking minutes or even hours. Batch.Works have spent years developing a print method to address this and the result is a part aesthetic with distinctly visible layers. Embracing this, we’ve created a bold, playful design language that is accessible without being immature and combines geometric shapes with soft surfaces. The colour palette was carefully selected, with timeless tones juxtaposed with rich colours and each colour possibility resulting in a complimentary palette.
Collaborating with Batch.Works allows for the local production of short supply chains that offer: reduced transportation costs, improved transparency, and increased agility in responding to customer demand. Each pair of headphones can be printed so that children can effortlessly customise the multiple components with a range of colours to choose from. The material used to manufacture the plastic components are made from recycled PLA created from packaging waste from the agricultural industry using a unique fused deposition modelling method, paired with the use of TPU for softer components such as the headband cushion.
Batch.Works are currently developing a technique for “embedding an invisible unique part identification into every item we produce, like adding DNA”. This would enable the manufacturer to track exactly which batch and material a part is made from, facilitating more “data-driven recycling” and “adding a traceable legacy to material as it moves from one form to the next.
“Kibu is proving that circular and replaceable consumer electronics is possible today”
- Jo Barnard, Morrama founder and creative director
Join the waiting list to find out about our upcoming launch in Q2 2024 at kibu.family.